Reducing Emissions is Necessary but not Sufficient
As the international community heads for Glasgow and their 26th climate conference, the latest report of the Intergovernmental Panel on Climate Change is not encouraging. The report concludes that unless there are immediate, rapid and large-scale reductions in greenhouse gas emissions, limiting climate warming to 1.5°C or even 2°C will not be possible.
The International Energy Agency predicts that global energy demand, a tell-tale indicator of future emissions, will rise 5% in 2021 and a further 4% in 2022. In its Sustainable Recovery Tracker, the IEA estimates that current policies put global carbon dioxide emissions on track to set a new record in 2023 and to continue to grow in following years, with “no clear peak in sight.”
In lockstep with rising greenhouse gas emissions, the effects of a warming climate have been on full display, with more severe storms, extreme drought, wildfires and flooding. We clearly need to reduce emissions, and quickly, yet climate science now shows that emission management by itself will not be enough to keep climate warming below 1.5ºC, or even 2ºC. Not only is the global community slow to change course to a low emissions economy, but also there are emissions sources that will be very difficult to decarbonize – aviation, land and sea shipping, and steel production, for example.
Since the 2018 IPCC 1.5ºC report it has been evident that removing carbon from the atmosphere is an essential element of plans to reach net-zero emissions. The amount of carbon removal needed will depend on how fast we reduce emissions. Moreover, given that we are increasingly likely to overshoot the 1.5ºC goal, enough carbon removal to produce “net-negative” emissions — CO2 removal exceeding CO2 emissions — will be needed to compensate for the overshoot.
Negative Emissions
There are a range of natural and technological solutions to generate “Negative Emissions” (NE). Natural solutions include afforestation, soil management, CO2 mineralization, and ocean alkalinity enhancement, to name a few. The problem with natural solutions is twofold. Given the magnitude of our emisssions problem, natural solutions by themselves are not sufficient to generate negative emissions at the necessary scale — tens of gigatonnes (that’s tens of billions of metric tons) per year by 2100. Secondly, storing captured carbon above the ground in biomass is “not a durable carbon removal solution,” as we saw with the amount of forest and peatland damaged in this summer’s wildfires in Siberia and the western U.S.
Technological solutions may be able to close the NE gap.
You may recall Carbon Capture and Storage (CCS) was a key technology in our earlier post on the U.S. climate strategy to reach net zero emissions. By itself, CCS is an emissions reduction technology – CO2 is captured at the emissions source (e.g., the factory smokestack), condensed to liquid form and shipped off to storage. Ideally, the captured CO2 is sent via pipeline to a geological storage site, where it is compressed and injected down a well, deep underground. This is a viable emissions reduction strategy, using existing technology, that is ideally suited for high volume, point source emitters, such as fossil fuel power plants. In those situations, where CO2 is present in relatively high concentrations, CCS can capture carbon dioxide at a cost of about $40 per tonne.
But CCS is not a universal solution. Pipelines to the vast number of point sources of CO2 emissions is clearly infeasible, and other methods of transport are much less efficient. Also, CCS is not feasible for decentralized emissions sources like aviation and ocean shipping. Low emissions fuels for such applications are still in the laboratory stage. However, CCS is a key element of another emerging Negative Emissions technology — Direct Air Capture with Carbon Storage, or DACCS.
Direct Air Capture Technology – a Silver Bullet?
Rather than capture CO2 at a point source of emissions, DACCS technology extracts CO2 that is already in the atmosphere. CO2 is essentially uniformly distributed throughout the atmosphere. although at a low concentration of about 0.04% by volume. Although the low CO2 concentration means that a DACCS facility needs to process a lot of air for each kilogram of carbon it extracts, it can be located anywhere on the planet. Thus, it is possible to locate the DACC plant at or near an existing geological storage site, or near an existing pipeline to the storage site. DACCS technology prototypes are currently in operation at 15 pilot plants worldwide, removing a total of 9,000 tonnes per year.
We need to be removing 10 Gt per year from the atmosphere (1 Gigatonne = 1 Billion tonnes) by 2050, and 20-30 Gt per year by 2100 to meet our climate goals. (The requirements later in the century are dependent on our success — or lack thereof — in controlling emissions.) So the questions we need to answer are:
- does the technology scale to meet our needs?
- what are the impacts of a DACC plant – land, energy and water requirements?
- what is the cost of implementing and operating the technology at scale?
How Does it Work?
Direct Air Capture technologies use a chemical process to extract CO2 from the air. The leading DAC implementations today use either synthetic solid sorbent (material that attracts CO2 molecules to its surface) or a water-based solvent as the CO2 capture agent. Fans pull air into an enclosure called the contactor, where it is exposed to the CO2 capture agent. Air circulation within the contactor is managed to allow enough time for the CO2 to move through the porous sorbent or the liquid solvent and bond with the capture agent. CO2 is later recovered by breaking the bonds, using heat or a combination of heat and other chemical reactions, leaving liquid CO2 and restoring the capture agent for reuse. The CO2 is compressed for transport to the underground storage site.
Two companies are far and away the leaders in DAC technology implementation – Climeworks, a Swiss company founded in 2009, and Carbon Engineering, a Canadian firm also founded in 2009.
Climeworks
Climeworks uses the synthetic solid sorbent approach, with relatively small, modular “collectors” (contactors). Air inside the collectors is forced over solid sorbent “filters” to trap the CO2 while the other components of the air are returned to the atmosphere. When the filter is full, the collector is closed and heated to between 80 and 100ºC, releasing the highly concentrated CO2, which is then collected and stored.
Climeworks’ flagship DACCS facility is its “Orca” plant in Iceland, currently the world’s largest complete capture and storage plant. Developed in partnership with Iceland’s Carbfix carbon storage company, Orca’s captured CO2 is mixed with water and injected into basalt rock formations deep underground. The CO2 reacts with the basalt in a natural mineralization process, eventually turning to stone. Making use of Iceland’s volcanic geology, the Orca plant is able to use geothermal energy to provide the heat required to release the CO2 from the collector filters. The Orca plant was commissioned in 2021, and is capable of capturing and storing 4,000 tonnes of carbon dioxide per year — roughly equivalent to the annual emissions from 870 cars, based on EPA estimates of 4.6 tonnes of CO2 per car. (The total number of cars on the planet is estimated to be 1.4 billion.)
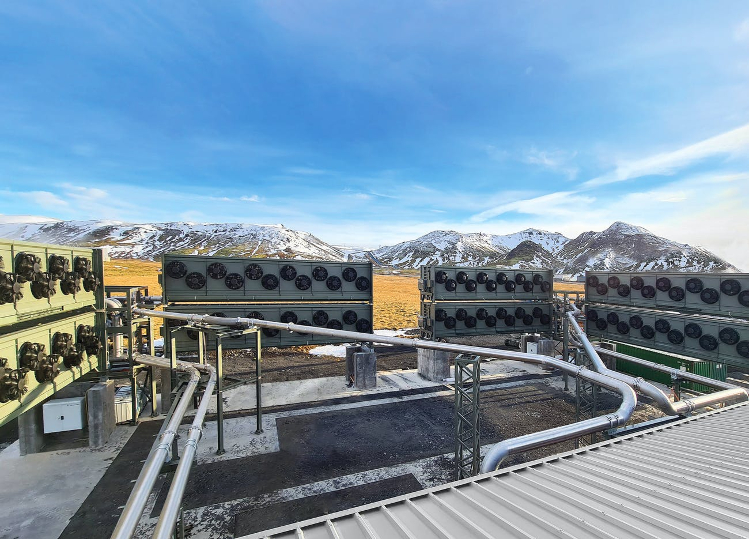
The Climeworks/Carbfix facility in Iceland. The modularity of the CO2 capture facility is clearly evident. Credit: Climeworks
While the capacity of the Orca facility seems underwhelming in the face of the need for gigatonnes of CO2 extraction, the plant does highlight the strengths of Climeworks’ technology. A major advantage is its modularity. The individual modules lend themselves to mass production, with the associated economies of scale. The low heat requirements of the solid sorbent process is easily provided by geothermal heat, industrial waste heat, or concentrated solar heating. The system does not require water, in fact the process actually extracts a small amount of water from the air. The modular design can be scaled up or down for a wide variety of sites.
As a business, Climeworks is currently generating revenue by selling carbon offsets. Bloomberg reports that the base price for offsets is $1,200/tonne, although volume purchasers pay less. (Bill Gates, a major supporter of Climeworks, reportedly paid $544/tonne.) Major customers include Microsoft, Stripe, The Economist, Accenture, Shopify and Swiss Re. Demand is so high that Climeworks have already started planning a new facility ten times larger than Orca, to go online in about three years. Climeworks expects to be able to drive prices down to $200-$300 per tonne by 2030 and ultimately to the $100-$200 range. With the EU carbon price expected to rise to more than $100, Climeworks is heading in the right direction to make its DAC approach economically feasible.
Carbon Engineering
Carbon Engineering is a Canadian company founded in 2009. Their first pilot plant started operations in 2015 and used captured CO2 as a feedstock to generate a near carbon neutral synthetic fuel in what it calls its “Air to Fuels” process. Climate Engineering uses the liquid solvent approach to capture CO2. Unlike Climeworks, Climate Engineering has adopted an “industrial scale” engineering approach to DAC plants from the outset, clearly seen in the following picture of its current product development facility in British Columbia.
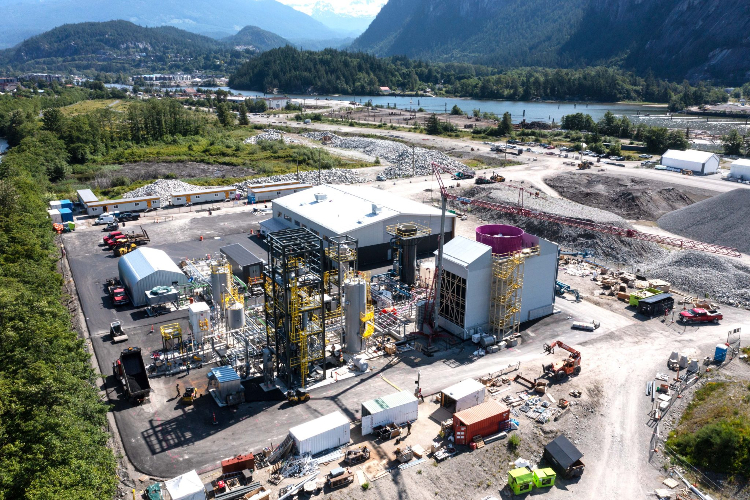
Carbon Engineering’s product development facility in Squamish, British Columbia Credit: Carbon Engineering
Carbon Engineering’s DAC technology has four major pieces of equipment that have been widely used in large-scale industries for years.
Like the Climeworks system, the process starts with an air contactor – in this case a large structure modelled after industrial cooling towers. A giant fan (located under the large purple ring in the photo above) pulls air into this structure, where it passes over thin plastic surfaces that have the solvent solution flowing over them. The CO2 captured in the solvent solution is then put through a series of chemical processes to increase its concentration, purify and compress it, so it can be delivered in gas form ready for use or storage. This involves separating out the salt formed in the solution when the CO2 binds with the solvent, forming small pellets in a structure called a pellet reactor. This step is adapted from proven water treatment technology. The pellets are then heated to about 900ºC in a Calciner, another proven industrial process, releasing the CO2 in pure gas form. This step leaves behind processed pellets that are hydrated in a Slaker and recycled back into the system to reproduce the original capture chemical.
By using technology that is already used in large-scale industrial applications, Carbon Engineering plans to build facilities capable of capturing millions of tonnes of CO2 per year, with low scale-up risk and relatively low cost. The drawbacks of the Carbon Engineering approach are the requirements for water to manufacture the solvent, much of which is lost to evaporation, and the energy required to generate the high temperatures in the Calciner. Using natural gas with carbon capture solves the latter issue.
Carbon Engineering’s industrial-scale DAC plants will typically be located at or near a geological storage facility, or near an existing CO2 pipeline. Going forward, Carbon Engineering is licensing its technology to partners with existing carbon storage facilities.
The first such partnership is with 1PointFive, a development company supported by Occidental Petroleum. The companies are jointly engineering the facility shown in the graphic below, which is expected to be the world’s largest Direct Air Capture facility. Colocated with Occidental’s CO2 underground storage facility in Texas, it will capture one million tons of CO2 per year (1 Megatonne/year) when complete. Further extending our vehicle emissions comparison, a Megaton per year is equivalent to the annual emissions of about 215,000 cars. Engineering and design is underway and construction will begin in 2022. 1PointFive is planning to build dozens of plants in Texas’ Permian Basin.

1PointFive plant scheduled for construction in 2022. Credit: 1PointFive
Earlier this year, Carbon Engineering also announced a partnership with UK firm Storegga, and engineering has begun on a 0.5 – 1 Mt/year DAC facility that is scheduled to go live in 2026. The Storegga plant will be located in northeast Scotland and will use existing pipelines to store CO2 beneath the North Sea.
Carbon Engineering estimates that economies of scale will push down the cost of CO2 capture and storage using its technology to about $94 per ton.
So, Do We Have a Solution?
Yes, and No. Current scientific estimates are that we will need to remove 10 GigaTonnes (10 billion tonnes) of CO2 per year by 2050, increasing to 20-30 Gt per year by 2100. Achieving the 2050 goal with Carbon Engineering’s 1 Mt per year plants will require 10,000 installations, at an estimated cost of $500M each, for an eye-watering total of $5 trillion.
There isn’t a commercial market for that much CO2, so government policies will have to fund DAC operations. The EU solution of carbon taxes and tariffs is an obvious choice. Government investment in technology development and maturation is another necessary step. In the carbon tax-shy U.S., alternative policies will be necessary to fund DACCS operations.
As mentioned earlier, natural negative emissions solutions can soften the blow somewhat, but they won’t make much of a dent in the 10 Gt per year requirement. Of course, this also assumes full implementation of the Paris Agreement’s aggressive emissions reductions — far from a sure thing. It looks like we have no alternative to making DACCS work.
Counting on DACCS technology has two unanswered risks. First, although the key elements of DAC plants are well understood, with virtually off the shelf solutions, the end-to-end process is still under development, and operations and maintenance costs are not well understood. Requirements for provisioning a 10,000 unit fleet of DAC plants with the required energy and chemicals will be a challenge, for example. Second, there is a risk that industry may seize upon future DACCS solutions as a replacement for emissions reduction now — leaving us high and dry if DACCS doesn’t work out.